Hey everybody, a new material weekly on surface grinding of ultra-fine cemented carbides. Reading this probably cost you about 15 minutes
Abstract of this article: The grinding experiment of superfine cemented carbide was carried out on a plane grinder with diamond grinding wheel. The grinding surface morphology was observed by scanning electron microscopy and the surface roughness was measured by surface roughness tester. The influence of grinding parameters on the surface roughness of ultra-fine cemented carbide grinding was analyzed. The results show that the grinding surface roughness of superfine cemented carbide increases with the increase of grinding wheel size at the same cutting depth. When grinding with the same grain size grinding wheel, the surface roughness of ultra-fine cemented carbide grinding increases with the increase of the cutting depth. When the cutting depth increases to a certain value, the surface roughness decreases gradually.
girii?
WC-Co cemented carbide is a conventional tool material. In recent years, with the continuous development of cutting technology, the requirements for the strength, hardness and wear resistance of tool materials are getting higher and higher. Compared with traditional structural cemented carbides, superfine cemented carbides (WC grain size 0.1-0.6 um) have higher strength, hardness and wear resistance, so they are widely used in tool manufacturing industry.
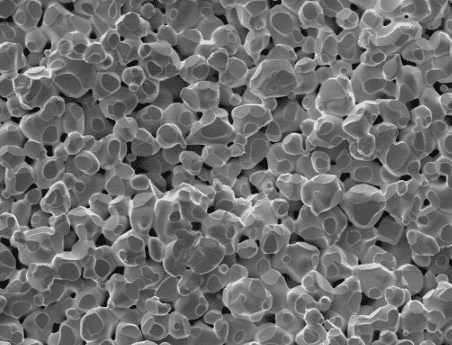
Grinding with a diamond grinding wheel is the main method to produce cemented carbide tools. Many studies have shown that grinding surface roughness has an important influence on the cutting performance and service life of cemented carbide tools. Up to now, the grinding research of cemented carbide at home and abroad mostly focuses on the improvement of traditional structure cemented carbide grinding process and surface quality control, while the grinding process of superfine cemented carbide, especially the grinding surface roughness, is rarely studied. Therefore, through grinding experiments, the influence of grinding wheel size and cutting depth on surface roughness of ultra-fine cemented carbide grinding is discussed by means of scanning electron microscopy (SEM) and surface roughness tester, in order to provide the basis for the optimization of grinding process of ultra-fine cemented carbide.
Test materials and methods
Test materials
The test material is ultra-fine grain WC-Co cemented carbide sintered by HIP technology. The sample size is 10 mm x 10 mm x 10 mm. The chemical composition and mechanical properties are shown in Table 1.
Table 1 Chemical composition and mechanical properties of test materials
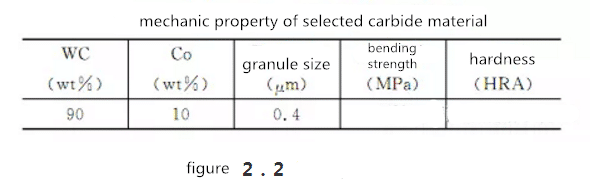
The samples were clamped with precision flat clamp and ground on the surface grinder Model M7120. The grinding wheel used is resin bonded diamond flat grinding wheel with an outer diameter of 250 mm, a width of 25 mm and a diamond layer thickness of 8 mm. The coolant is a mixture of water and emulsified oil. The experimental grinding parameters are shown in Table 2.
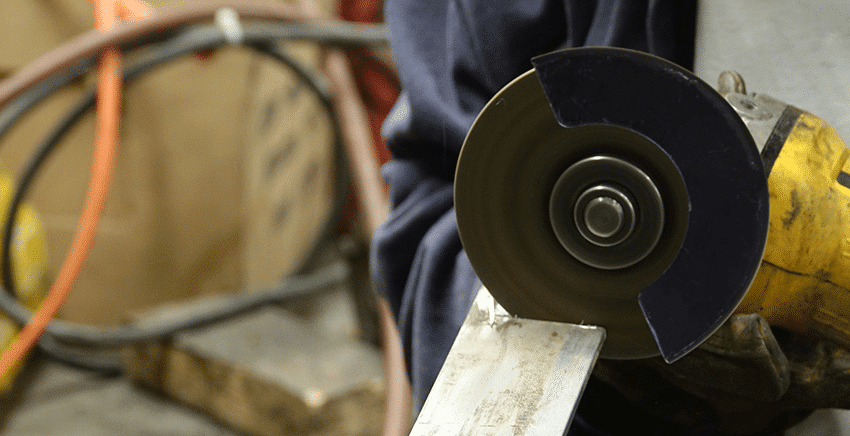
After grinding test, samples were cleaned with anhydrous acetone in the ultrasonic cleaner for 30 minutes and dried by hot air. Scanning electron microscopy with back reflection detector was used to observe the grinding surface morphology of the sample. The grinding surface roughness of the sample was measured along the direction perpendicular to the grinding direction with the surface roughness tester. The sampling step was 0.25 mm, and the evaluation length was 4 times of the step. Each sample was measured six times and the results were averaged.
test result
Fig. 1 shows the variation of grinding surface roughness with grinding wheel size under the same cutting depth (ap=10 um). It can be seen from the graph that the grinding surface roughness increases with the increase of grinding wheel size at the same cutting depth. But the influence of grinding wheel particle size on surface roughness is different. Compared with 150 # grinding wheel, using 280 # grinding wheel, the change of surface roughness is smaller while using W20 grinding wheel, the change of surface roughness is larger. Figure 2 shows the variation of surface roughness with the depth of cut AP when grinding with the same grinding wheel (150 #). It can be seen from the graph that the roughness of the grinding surface increases approximately linearly with the increase of AP when AP is less than 15 micron. But when AP > 15 um, the grinding surface roughness decreases gradually with the increase of shear depth, which is obviously different from the grinding test results of traditional structure cemented carbide.
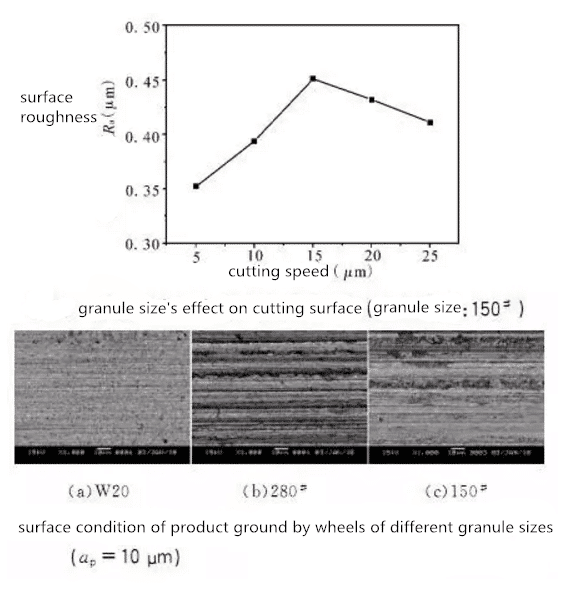
Surface roughness is the direct reflection of grinding surface morphology. In order to analyze the causes of the above parameters affecting the grinding surface roughness of ultra-fine cemented carbide, the surface morphology of grinding samples was observed by SEM with back reflection electron detector. Figure 3 shows the back-reflection electronic image of the grinding surface morphology of the sample ground with different diamond grinding wheels under the same cutting depth. As can be seen from the figure, the grinding marks on the surface of superfine cemented carbide ground by W20 grinding wheel are narrow and shallow, the bottom and sides are smooth, and the uplifts on both sides are very small (see Figure 3a). After grinding with 280 # grinding wheel, cracks appear on the grinding surface. The grinding marks are wide and deep, and the bottom and sides are rough with scaly fracture structure (see Fig. 3b). After grinding with 150 # grinding wheel, although the depth of grinding marks on the grinding surface is relatively shallow, there are more grinding debris and fracture structure (see Figure 3c), showing obvious brittle fracture characteristics.
Analysis and discussion
Grinding is accomplished by a large number of high hardness Abrasives arranged randomly on the surface of the grinding wheel. Each abrasive grain can be regarded as a tiny cutter approximately. The grinding surface is formed by the relative motion of these numerous irregular cutting micro-edges on the surface of the ground material. Therefore, the grinding wheel size, cutting depth and mechanical properties of the ground material will inevitably affect the grinding surface morphology, and then affect the grinding surface roughness.
Before the test, the sharp diamond abrasives can be simplified into cones because the same dressing method and material are used for each wheel. At the same time, due to the high stiffness of grinding machine system and the cooling effect of grinding fluid, the thermal deformation of diamond grinding wheel in contact with the sample during grinding can be neglected, and the actual cutting depth can be replaced by the set cutting depth of the grinding wheel. Then, in the process of plane grinding, the radial grinding force Fp exerted by grinding wheel and the maximum cutting thickness Hm of a single abrasive grain can be obtained by formula (1) and formula (2), respectively.
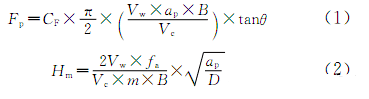
In the formula, CF is a constant related to the type of material being ground; Vw is the speed of workpiece, m/min; Vc is the speed of grinding wheel, m/s; B is the width of grinding, mm; theta is the half-angle of cone top of abrasive grain; AP is the set cutting depth, micron; FA is the axial feed, mm; m is the effective number of abrasive grains per unit area of grinding wheel. D is grinding wheel diameter, mm.
The removal mechanism of hard and brittle materials such as cemented carbide and ceramics usually includes inelastic deformation removal, brittle removal, and material powdering, etc. It depends on the force condition of grinding surface during grinding. When the normal load on the surface of the ground material below the abrasive grain is lower than the critical value of cracks in the material, the ground material is removed by non-elastic deformation such as sliding, plowing and chip formation. When the normal load on the grinding surface exceeds the critical normal load on which the material cracks occur, the grinding cracks nucleate and gradually extend to the grinding surface, and the material is removed by brittle means such as peeling and fragmentation. The harder phase in the material will be powdered under larger normal load. The low hardness bonding phase will be coated on the surface of the powdered hard phase and partially removed with the hard phase debris.
In the grinding process of cemented carbide, the critical normal load produced by cracks and debris can be expressed as
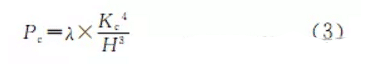
In the formula, lambda is a comprehensive constant, lambda_2*105; H is the hardness of the material; Kc is the fracture toughness. Formula (1) shows that under the same grinding conditions as wheel speed, workpiece speed, grinding width and axial feed, the normal grinding force Fp on the surface of the ground material is proportional to the cutting depth and increases linearly with the increase of ap; Formula (2) shows that the maximum cutting of a single abrasive particle is achieved. The thickness increases with the increase of AP and decreases with the increase of effective abrasive number M.
In this experiment, under the same cutting depth (i.e. the same Fp), the normal loads exerted by a single abrasive on the surface of the ground material are also different due to the different particle size of the diamond grinding wheel. Due to a large number of effective abrasives, the normal load exerted by a single abrasive on the grinding surface is small. Therefore, when superfine cemented carbide is ground by W20 grinding wheel, its removal mode is mainly inelastic deformation. At the same time, due to a large number of effective abrasives, the maximum cutting thickness Hm of a single abrasive is relatively small, and only slight friction and plowing occur on the grinding surface, so the grinding surface has narrow and shallow grinding marks, smaller uplift (see Fig. 3a), and lower surface roughness. With the increase of grinding wheel size, the number of effective abrasives decreases, and the normal load exerted by a single abrasive on the grinding surface increases. When the load is larger than the critical normal load of the crack-fragment of superfine cemented carbide material, cracks and cracks begin to appear on the grinding surface (see Fig. 3b). With the increase of grinding wheel size, the degree of cracking becomes more serious (see Fig. 3c). The main way of material removal is brittle removal. Compared with slip friction and slight plow, cracks and cracks seriously deteriorate the roughness of grinding surface, which is reflected in the measurement value of surface roughness. The roughness of grinding surface decreases with the increase of grinding wheel size (see Fig. 1). It is precise because of the difference of material removal methods that the surface roughness of grinding surface varies greatly when grinding with W20 grinding wheel.
When grinding with the same grinding wheel and different cutting depth, the normal grinding force Fp of the grinding wheel increases with the increase of the cutting depth, and the normal load on the grinding surface increases with the increase of the single grinding particle, which makes the material removal mode of the grinding surface of ultra-fine cemented carbide change. When the cutting depth AP is less than 5 micron, the normal load exerted by a single abrasive particle on the grinding surface is small. The material removal mode during grinding is mainly plowing in inelastic deformation, which produces deep grinding marks on the surface and has higher uplift on both sides. When AP (> 10 um), the material removal mode gradually changes to brittle removal mode, resulting in cracks and cracks on the surface, which become more and more serious with the increase of cutting depth, so the grinding surface roughness gradually increases with the increase of cutting depth. However, when AP > 15 microns, the surface material of superfine cemented carbide grinding begins to powder and evenly smeared with Co phase, and the roughness value of grinding surface decreases gradually (see Fig. 1).
According to formula (3), the critical normal load of grinding crack nucleation of cemented carbide is related to the physical and mechanical properties of the material itself. The higher the fracture toughness or the lower the hardness of the material, the greater the critical normal load Pc of grinding surface cracking. Compared with the conventional structure cemented carbide with larger WC particle size, the ultra-fine cemented carbide has higher hardness and lower fracture toughness, and its Pc is much smaller in the grinding process. Under the same grinding conditions, the grinding surface of ultra-fine cemented carbide is easier to produce powdering. Therefore, when the cutting depth reaches a certain value, the roughness of the grinding surface decreases gradually, and the Pc is much smaller in the grinding process. Under the same grinding conditions, the grinding surface of ultra-fine cemented carbide is easier to produce the powder. Therefore, when the cutting depth reaches a certain value, the roughness of the grinding surface decreases gradually.
son s?zler
(1) Under the same cutting depth, the grinding surface roughness of superfine cemented carbide increases with the increase of grinding wheel size. The surface roughness is low when grinding with a fine diamond grinding wheel.
(2) When grinding with the same size grinding wheel, the surface roughness of ultra-fine cemented carbide grinding increases with the increase of the cutting depth. When the cutting depth increases to a certain value, the grinding surface roughness decreases gradually.
(3) The influence of grinding parameters on the surface roughness of ultra-fine cemented carbide grinding can be attributed to the difference of material removal methods during grinding.
This is this week’s material weekly. I hope it will be helpful to you.