Under the background of increasing difficulty in improving engine technology and unsatisfactory power battery efficiency, lightweight technology is a common basic technology for both traditional fuel vehicles and new energy vehicles. As a lightweight material with many excellent properties, aluminum alloy has become the preferred material in the development of automobile lightweight technology.
The body mass accounts for about 40% of the total vehicle mass. For the lightweight of the whole vehicle, the lightweight of the body plays an important role.
Today, let’s talk about the key manufacturing technologies of aluminum alloy parts for automobile body, including hydroforming technology of aluminum alloy automobile plates and pipe fittings, warm stamping technology of plates, extrusion forming of profiles and casting (aluminum casting) forming technology of structural parts.
Application of aluminum alloy in car body
The grades of aluminum alloys are divided into nine series from 1000 to 9000 according to the types and contents of non aluminum elements.
Aluminum alloy materials for automobile body mainly include: 2000 series with the highest content of copper and high hardness, 5000 series mainly containing magnesium and also known as “magnesium aluminum alloy”, 6000 series with high content of magnesium and silicon and good corrosion resistance and oxidation resistance. Aluminum alloy materials such as plates, profiles, pipes and high-performance cast aluminum of different series models will be used in different stress parts of automobile body.
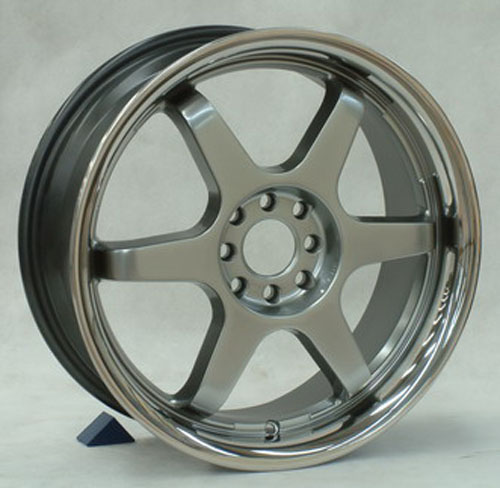
Aluminum alloy is widely used in automobiles
Aluminum castings are made into parts that can carry large loads, which obviously reduces the weight but also has high strength. These plates have complex geometry and are usually vacuum die cast to make them have high strength. Aluminum castings also have high ductility, good welding performance and high plasticity, which ensure high safety in case of collision. The aluminum alloy type of these castings is 5000 or 6000 series aluminum alloy. At present, aluminum castings are mainly used in the structural box of electric vehicle battery pack.
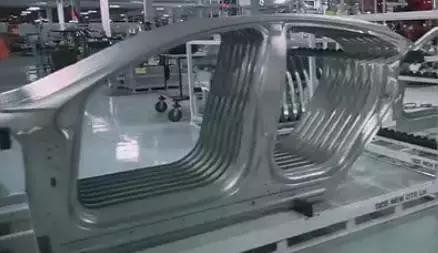
Tesla Model s battery box
Key manufacturing technology of aluminum alloy parts for automobile body
Aluminum alloy parts for automobile body mainly include cast (cast aluminum) connectors, covering parts (sheet stamping), extruded profile frame structural parts, hydroforming sheet metal covering parts and pipe structural parts.
The surface quality of aluminum alloy processed by ordinary stamping process is poor and the yield is low (only about 70%), which can not meet the requirements of high precision, high reliability, high efficiency and low defect manufacturing of body parts. The hydroforming technology of automobile body parts has been widely used in the automobile industry in developed countries such as Europe, America, Japan and South Korea. The maximum pressure of the equipment has reached 400 MPa. Aluminum alloy automobile hood inner and outer panels, door inner and outer panels, fender and other panels have been processed and put into use.
Large aluminum castings and hydroforming parts are two core technologies of aluminum alloy forming. The hydroforming process of aluminum alloy automobile sheet and pipe is shown in the figure below.
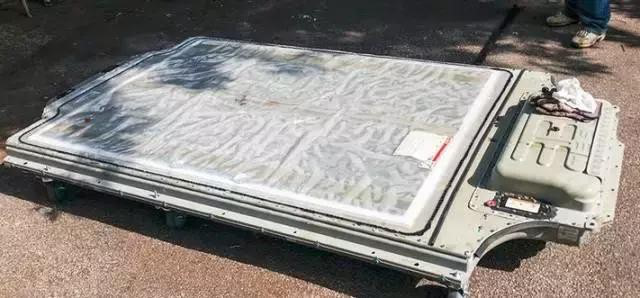
Hydraulic forming process
Compared with the stamping process, the advantages of hydroforming process are as follows:
(1) Reduce the blank size and save materials;
(2) Improve forming limit and reduce forming passes;
(3) The surface quality and dimensional accuracy of parts are greatly improved;
(4) Reduce the number and cost of supporting molds;
(5) Reduce the amount of subsequent machining and assembly welding;
(6) It can form parts with complex shape, large deformation degree and high integrity requirements.
This technology has become the mainstream technology of automobile lightweight abroad, and is developing towards integration, rapidity, large-scale, accuracy and so on. Although the development of large tonnage hydroforming prototype has been successful in China, such as 1600 T and 1050 t material Hydroforming Equipment, there are still the following main difficulties in popularizing and applying aluminum sheet hydroforming technology in China:
(1) Based on the lack of knowledge of aluminum sheet hydroforming design. The hydroforming knowledge provided to designers is not systematic and comprehensive, which makes Chinese designers unable or unable to consider the application of hydroforming technology in lightweight structural parts.
(2) The research of Aluminum Sheet Formability and part quality control system for hydroforming technology is insufficient. Most of the research results of Aluminum Sheet Formability and part quality control for ordinary stamping are not suitable for hydroforming technology.
(3) Many key technologies of tooling and mould and ultra-high pressure hydraulic source system facing industrialization need to be broken through.
(4) The research on the whole system linkage equipment with aluminum sheet hydroforming as the core is not perfect.
Due to the above reasons, the industrialization oriented parallel action system has not been applied in practice. It is difficult to develop tooling and mold and has a long debugging cycle. Therefore, the cost is high, and it is still rarely used in domestic models.?
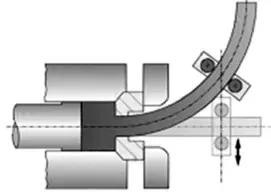
Hydroforming application of aluminum alloy automotive sheet parts (Tesla Model s side wall and floor)
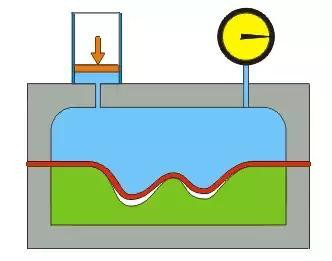
Application of internal high pressure forming of aluminum alloy automobile pipe parts (Tesla Model s p85d and Jaguar XFL)
The warm forming process of aluminum alloy sheet is affected by many factors, such as material formability, process parameters and die design, lubrication and friction state. At present, it is still a new sheet metal stamping technology to be further studied and developed. If a breakthrough is made, high-efficiency forming technology can be provided – an average of more than 540 parts per hour (ASPH).
Warm stamping process of automobile floor
In recent years, aluminum alloy sheet warm forming technology has been applied to automobile body. At present, there are still some deficiencies in the application of sheet warm forming stamping technology in body aluminum stamping, mainly in the following aspects.
(1) Formability needs to be further improved. The local drawing property of aluminum alloy sheet is not good, and it is easy to produce cracks, especially for parts with complex shape.
(2) The surface quality of parts is not ideal. In order to avoid tensile cracking, it often leads to insufficient stamping and stretching, and as an outer panel, it is prone to local surface distortion and other defects, affecting the surface quality.
- The dimensional accuracy is not easy to master and the springback is difficult to control. Due to the above reasons, the development of aluminum sheet stamping die is difficult and the commissioning cycle is long, so the cost is high and it is difficult to meet the quality requirements of high-end car body parts.
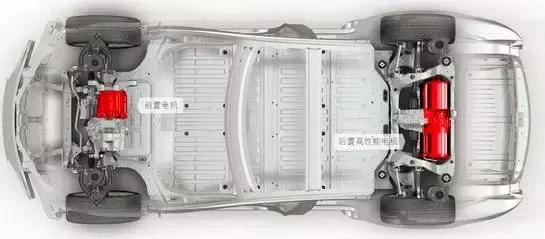
Automobile outer panel
Profile extrusion
In the body design, the application of space frame design can increase the static torsional stiffness of the body by 60%. Profile extrusion technology is a servo controlled extrusion bending integrated forming technology of body frame profile, and it is also the main technical means to realize space frame design.
Germany, Japan and the United States have invested a lot of manpower and material resources to tackle key technologies such as extrusion process, precision quenching and artificial aging, finishing and straightening of large flat and wide aluminum alloy profiles. Some new extrusion technologies have also been developed, such as high-speed extrusion, hydrostatic extrusion, no residue extrusion, variable section extrusion and so on.
Medium and high-end vehicles, such as many models of Audi and BMW, Nissan series, general Regal and Grand Hyatt, Toyota Crown, etc., all use aluminum alloy as the material of anti-collision beam and energy absorption box.
The extrusion process of profile actually starts from product design. The use requirements of the product determine many final parameters of the product, such as machining performance, surface treatment performance and service environment requirements, which determine the type of extruded aluminum alloy. The design shape of the product will also determine the performance of aluminum profile and the shape of extrusion die.
When the design problem is solved, the actual extrusion process starts with the aluminum casting rod for extrusion, which is heated and softened before extrusion, and then put into the ingot holding cylinder of the extruder. Then, the front end is driven by the high-power oil cylinder, and the extrusion pad and extrusion rod are installed at the front end. Under the action of strong pressure, the softened aluminum casting rod is extruded from the precision forming hole of the die.
Extrusion bending integrated processing technology is shown in the figure below. The bending deformation of profile after die exit is realized by a series of guiding devices. This method can not only accurately control the bending accuracy of profile, but also easily realize three-dimensional bending (that is, different parts have different bending directions and radius of curvature). The distance between the bending guide die and the extrusion die outlet can also be adjusted according to the stress conditions when the profile is bent.
Profile extrusion bending integrated processing
In terms of extrusion process, the optimization of process parameters is difficult to achieve because the motion characteristics of ordinary extrusion press are fixed. The combination of servo control system and extrusion press can realize the motion characteristic curve of any slider, the position accuracy of slider can reach 0.01mm, and the stroke of servo press can be easily adjusted according to the needs of forming process, which is of great significance to improve product quality and production efficiency and reduce production cost.
For the section changing structures such as the front longitudinal beam, seat rail, bumper and damping structure of the automobile, the forming process usually adopts stamping welding method, extrusion and bulging forming. These processes are complex, low production efficiency and high cost, and the welding parts will reduce the body stiffness and energy absorption characteristics. The servo controlled extrusion bending integrated forming method is used to manufacture the aluminum profile components in the above structure, which can significantly reduce the subsequent machining amount of semi-finished products and obtain all fiber high-performance extrusions, so as to improve the strength performance and reliability of the body frame.
Casting (aluminum casting) forming technology of structural parts

Aluminum alloy body frame structure (ASF)
The body frame of aluminum alloy body frame structure is composed of cast and hydroformed aluminum alloy parts, including 35% high-precision aluminum alloy castings, 22% extruded aluminum alloy parts and 35% aluminum alloy plates. Among them, most of the connectors of the body frame are aluminum alloy castings. These castings play the role of connecting all aluminum materials of the body. They are the main load-bearing components and should have high strength. In order to meet the needs of use, most of the body aluminum alloy castings are complex thin-walled structures. Due to the structural characteristics of such castings and the needs of mass production in the automotive industry, the traditional casting process can not meet the requirements. At present, foreign aluminum alloy body castings mostly use new squeeze casting processes such as vacuum pressure casting and special squeeze casting.
Vacuum pressure casting and special squeeze casting are new casting technologies. Compared with ordinary die casting, vacuum pressure casting increases the vacuum pumping operation, which can extract the gas in the mold cavity. The liquid metal fills the mold cavity in the vacuum state, reducing the involved gas. The casting can be heat treated, and the mechanical properties are higher than those of ordinary die casting. Special squeeze casting can not only realize the extrusion molding of liquid metal, but also the extrusion molding of semi-solid metal slurry. This slurry has good fluidity and spherical microstructure, and can form more complex castings. Moreover, the castings have excellent mechanical properties and high near final forming degree.
Reliable connection technology of aluminum body
Mechanical connection technology: aluminum alloy has high thermal conductivity. The traditional resistance spot welding technology is used for connection, with high energy consumption, and the quality is difficult to guarantee. At present, a large number of foreign automobile manufacturers use mechanical connection methods such as self punching riveting and self cutting screws to realize aluminum alloy connection.
Welding technology: for the connection technology of aluminum body parts, at present, in addition to a large number of non melting connection methods such as locking riveting, self cutting screw, self tapping screw, punching process and glue (bonding), there are also a large number of melting welding methods such as MIG welding, laser welding (including laser fusion welding and laser brazing) and laser MIG arc hybrid welding. Among them, MIG welding, laser welding, laser MIG arc hybrid welding and friction stir welding have become the standard welding processes for aluminum body parts.
Flexible edging Technology: the appearance quality of body panels is required to be high and the precision control is strict. The traditional molding edging investment is large and the flexibility is poor. The robot rolling process has become the inevitable trend of flexible edging. Many mature foreign automotive equipment suppliers already have flexible aluminum alloy edging technology, such as ThyssenKrupp of Germany, hirotec of the United States, EDAG of Germany, DVA of the United Kingdom and other companies. At present, the domestic suppliers of edging equipment for aluminum alloy panels are mainly European and American enterprises.
Automobile lightweight is an important development direction of automobile in energy conservation, environmental protection and pollution reduction in the future. As a typical lightweight material, aluminum alloy is more and more recognized by the industry, so it will be more and more widely used in automobiles. It can be said that all aluminum body will be a trend of automobile lightweight development in the future.