Tokarka to klasyczny temat w naszej bran?y obróbki skrawaniem. Ale czy znasz histori? rozwoju tokarek? Jakie t?o historyczne i zbiegi okoliczno?ci doprowadzi?y do ich powstania? Ten artyku? mo?e da? Ci odpowied?.
The prototype of lathes
The reason why humans evolved from apes is thanks to our hands. However, hands alone are not enough, so tools are necessary to assist in the process. Our ancestors were clever, and in order to facilitate the use of tools for processing, the earliest prototype of lathes, the wooden lathe, was born about two thousand years ago.
As a prototype, it was still quite rough, as you can see from the picture. When operating it, one would step on a loop below the rope, use the flexibility of the tree branch to rotate the workpiece, and use stone or shells as cutting tools to cut the object along the horizontal bar.
In the 13th century, the prototype of lathes was also developing. One could not always rely on trees. At this time, the “foot-operated lathe,” also known as the elastic pole lathe, was invented. The user would rotate the crankshaft with a foot pedal, which would drive the flywheel and then the main spindle, causing it to rotate. However, the operating principle was still the same as before, except that metal was used for the cutting tools.
A Frenchman named Besson in Europe designed a lathe for screw cutting that allowed the cutting tool to slide through the screw, which was achieved by the use of a screw thread. The cutting tool was no longer fixed in one position.
The prototype of the lathe at this stage has been introduced. Although the prototype continued to evolve, the power source still had not departed from the original wooden lathe. The continuous power supply was still a big problem, as even the most skilled humans would still experience fatigue.
Steam engines and lathes
As a steel master, Wilkinson invented the boring machine in 1774, which was the world’s first truly meaningful boring machine.
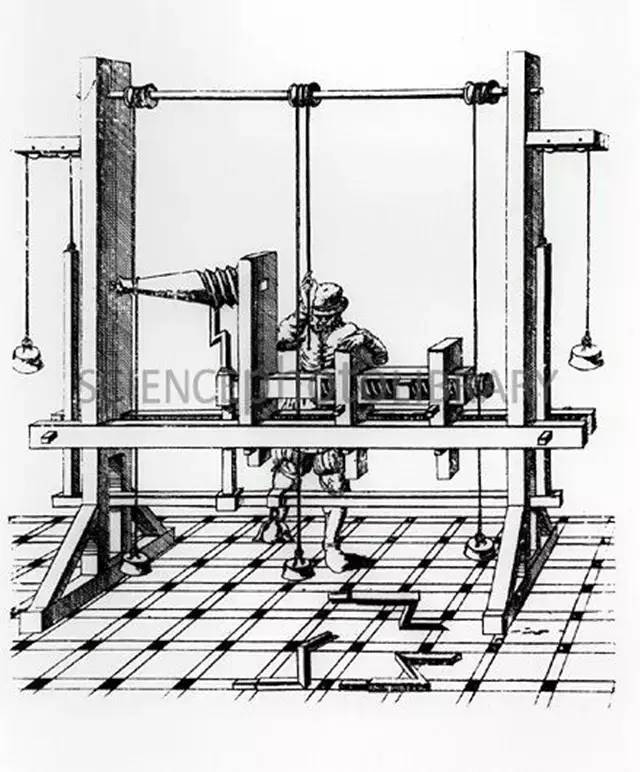
In 1775, Wilkinson used the cannon boring machine to bore the cylinder for Watt’s steam engine, which had numerous defects, to meet the requirements of Watt’s steam engine. Of course, as a businessman, Wilkinson also obtained the exclusive supply rights for the cylinder of Watt’s steam engine.
In order to bore larger cylinders, he also made a waterwheel-driven cylinder boring machine in the same year, which promoted the development of the steam engine. Since then, lathes began to be driven by steam engines through crankshafts. For both lathes and steam engines, they cooperated and promoted their mutual development. An era of industrial revolution reached its peak.
Lathe during the Industrial Revolution
The name of Maudslay is inseparable from lathes. In 1797, the father of the lathe industry made the first screw-cutting lathe, which had a lead screw and guide bars, and used a sliding tool holder – the Maudslay’s tool holder – and guides to cut threads of different pitches.
Afterwards, Maudslay continued to improve upon the lathe. In 1800, he created a lathe with a sturdy cast iron bed instead of the triangular iron bar frame, and used an idler gear with a change gear train instead of changing the pitch of the screw to cut different thread pitches. This was the prototype of the modern lathe and had significant importance to the Industrial Revolution in England.
Moving forward to the 19th century, due to the development of various industries, there was a need for different types of lathes. In 1817, Roberts invented the gantry lathe, while Whitney from the United States manufactured the horizontal milling machine. These two types of lathes were deliberately used for different industries’ part manufacturing needs. With the development of the Industrial Revolution, lathes continued to evolve.
One of the most accomplished mechanical engineers of the 19th century was undoubtedly Henry Maudslay. In 1834, he built a measuring machine that could measure to within one ten-thousandth of an inch. A year later, at the age of 32, he invented the screw-cutting lathe. He also recommended that all lathe manufacturers adopt a standard thread size, which became known as the Maudslay thread and was adopted as a standard by many countries.
In order to improve the degree of mechanization and automation, in 1845, Henry Maudslay from the United States invented the turret hexagonal lathe.
In 1873, American Spencer made a single-axis automatic lathe, and soon after he made a three-axis automatic lathe.
With the development of electric motors, lathes were upgraded from steam power to electric motor drive, marking another epoch-making improvement. We can see that the process from human power to water power, from steam power to electric power, has taken mankind several hundred years.
If we were to pick out those who have had an impact on all of our lives, we cannot ignore Henry Ford. A historian 100 years from now may conclude that Ford has had the greatest impact on all manufacturing industries worldwide, even to this day, because he pioneered a new method for producing cars.
Ford once proposed that cars should be “l(fā)ight, sturdy, reliable, and affordable.” To achieve this goal, it was necessary to develop efficient grinding machines. In order to achieve this, the American Norton company used diamonds and corundum to create large and wide grinding wheels with high rigidity and sturdy heavy-duty grinding machines in 1900. The development of grinding machines has brought the technology of mechanical manufacturing into a new stage of precision.
Improved manufacturing tools also contributed to changes in the manufacturing process itself, from producing one car in 12 hours to producing one car in 1 hour. In October 1908, the first standardized car, the Ford Model T, was driven off the assembly line.
In 1913, Ford revolutionized the entire process of assembling cars. Partially assembled cars hanging from ropes were pulled past workers who each assembled a single component. Soon, the Ford company was producing hundreds of thousands of cars per year, a remarkable achievement at the time, and this was the true birth of the manufacturing assembly line.
CNC Lathe machinine
After the end of the prolonged World War II, the manufacturing industry continued to maintain the pre-war level of development. Operators used manual controls on electric lathes to produce parts according to design drawings. Although this method of production was more efficient than the steam age, human beings are never satisfied.
The key question was how to achieve faster and more efficient production and how to solve some of the manufacturing’s unsolvable technical problems.
In the late 1940s, an American engineer named Parsons came up with a method of punching holes on a hard cardboard to represent the geometry of the parts that needed to be machined. He used the card to control the movements of the lathe. Although it was just an idea at first, Parsons presented it to the US Air Force in 1948. The Air Force was very interested because they were looking for an advanced machining method to solve the problem of machining aircraft model shapes.
Since the shape of the model was complex and required high precision, conventional equipment was difficult to adapt. The US Air Force immediately commissioned and sponsored the Massachusetts Institute of Technology to conduct research and develop this lathe controlled by a hard cardboard.
In the laboratory, a model of a numerical control lathe was developed. Finally, in 1952, Massachusetts Institute of Technology (MIT) and the Parsons Corporation collaborated to successfully develop the first demonstration machine, which used a large number of electronic tube components and its control device was even larger than the lathe itself.
Starting in 1960, countries around the world began to develop, produce, and use numerical control lathes. China developed its first numerical control lathe in 1968 at the Beijing No.1 lathe Factory. In 1974, microprocessors were directly used in numerical control lathes, which further promoted the widespread application and rapid development of numerical control lathes.
CNC lathes have also undergone six generations of development. The first three generations belong to the first stage, and the CNC system is mainly composed of hardware connections, called hardware CNC. The last three generations are called computer numerical control, and their functions are mainly completed by software. Starting from 1990, CNC lathes began to adopt universal CNC systems.