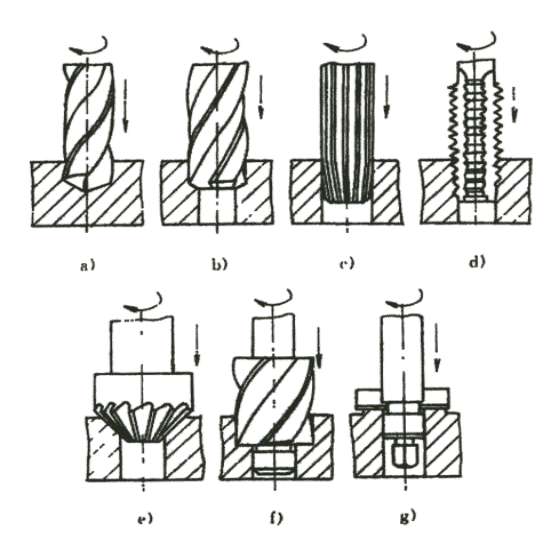
Drilling machine is a machine tool for machining internal holes. It is used to machine holes in solid materials. It is mainly used for machining workpieces with complex shapes and without symmetrical rotation axes, such as single holes on parts such as levers, covers, boxes and frames. Hole system. The drilling is rough machining.
? Process characteristics of drilling
(1) When the drill bit is cut in a semi-closed state, the amount of cutting is large,and chip removal is difficult.
(2) The friction is severe, generating more heat and making h
eat dissipation difficult.
(3) The high speed and high cutting temperature cause the bit to wear seriously.
(4) Squeeze is severe, the cutting force required is large, and it is easy to produce cold work hardening of the hole wall.
(5) The drill bit is thin and overhanging, and it is easy to bend and vibrate during processing.
(6) The drilling accuracy is low, the dimensional accuracy is IT13 to IT10, and the surface roughness Ra is 12.5 to 6.3 μm.·
???
??
Cutting process range
The drilling process has a wide range of processes. Different tools can be used on the drilling machine to complete the drilling center hole, drilling, reaming, reaming, tapping, boring and boring end faces, as shown in the figure. The drilling accuracy on the drilling machine is low, but the hole with high precision (IT6~IT8, surface roughness is 1.6-0.4μm) can also be machined by drilling—-reaming—-reaming hole. The fixture can be used to machine the hole system with position requirements.
When machining on the drill press, the workpiece is fixed and the tool moves in the axial direction (feed motion) while rotating (main motion).
Drilling Machine
The main types of drilling machines are: bench drilling machines, vertical drilling machines, radial drilling machines, milling and drilling machines, and center hole drilling machines. The main parameter of the drill press is generally the maximum bore diameter.
The vertical drilling machine is a widely used one in the drilling machine. It is characterized in that the spindle axis is vertically arranged and the position is fixed. The position of the workpiece needs to be adjusted so that the center line of the machined hole is aligned with the rotation center line of the tool. The main motion is achieved by the rotation of the tool while moving in the axial direction for the feed motion. Therefore, the vertical drilling machine is inconvenient to operate and the productivity is not high. Suitable for processing small and medium-sized parts in single-piece small batch production.
? Transmission principle of vertical drilling machine.
Main motion: single-speed motor is driven by gear stepping speed change mechanism; the rotation direction of the main shaft is changed by the motor’s forward and reverse rotation.
Feed movement: The spindle moves linearly with the spindle sleeve in the spindle housing. The amount of axial movement of the spindle is expressed by the amount of axial movement of the spindle per revolution of the spindle. Second, the bench drill. The bench drilling machine is referred to as a bench drill. It is essentially a vertical drilling machine for machining small holes. The structure is simple and compact, flexible and convenient, and suitable for processing small holes on small parts. The diameter of the borehole is generally less than 15mm.
Third, radial drilling machine
For workpieces with large volume and mass, it is very inconvenient to process on the vertical drilling machine. At this time, the radial drilling machine can be used for processing.
The headstock can be adjusted laterally along the guide rails on the rocker arm. The rocker arm can be adjusted along the cylindrical surface of the column and can be rotated around the column. During machining, the workpiece is fixed, and the position of the spindle is adjusted so that the center is aligned with the center of the hole to be machined and clamped quickly to maintain an accurate position. Radial drilling machines are widely used in single and medium and small batch production to process large and medium-sized parts.
If you want to machine holes and holes in any direction and at any position, you can use a universal radial drilling machine. The machine spindle can be rotated around a specific axis in space. There is also a lifting ring at the top of the machine that can be hung in any position. Therefore, it is suitable for processing large and medium-sized workpieces in single and small batch production.
Drilling Tools
twist drill
Structure of twist drill
The twist drill consists of three parts: the working part, the neck and the handle.
(1) Working part: The working part of the twist drill has two spiral grooves, and its shape is very similar to the shape of twist. It is the main part of the drill bit and consists of a cutting part and a guiding part.
?Handle
The handle is the clamping part of the drill bit, which is used to connect with the machine tool and transmit torque and axial force during drilling. The handle of the twist drill has two kinds of taper shank and straight shank. Straight shanks are mainly used for small twist drills with a diameter of less than 12 mm. The taper shank is used for twist drills with a large diameter and can be inserted directly into the spindle taper hole or inserted into the spindle taper hole through the taper sleeve. The flat tail of the taper shank is used to transmit torque and is used to easily remove the drill bit.
Neck
The neck groove of the twist drill is the overrunning groove of the grinding wheel when grinding the handle of the drill bit. The bottom of the groove is usually engraved with the specifications and the factory mark of the drill bit. Straight shank drills have no neck.
The composition of the cutting part
The cutting part is responsible for the cutting work and consists of two front faces, a main rear face, a rear back, a main cutting edge, a minor cutting edge and a chisel edge. The chisel edge is the edge formed by the intersection of the two mains, and the back is the two belts of the drill bit, which are opposite to the workpiece hole wall (ie the machined surface) when working, as shown.
The guiding portion is a guiding action when the cutting portion is cut into the workpiece, and is also a grinding portion of the cutting portion. In order to reduce the friction between the guiding portion and the wall of the hole, the outer diameter (i.e., on the two land) is ground with an inverted cone of (0.03 – 0.12) / 100. (0.03 to 0.12 reverse taper per 100mm length)
In addition, in order to improve the rigidity of the drill bit, the diameter of the core between the two blades of the working portion is made to be a positive taper of (1.4 to 1.8)/100 in the axial direction.
(1) rake face: the rake face is the surface of the spiral groove, which is the flow of chips through the surface, which acts as a chip and chip. It needs to be polished to make the chip removal smooth.
(2) Main flank: The main flank face is opposite to the machined surface and is located at the front end of the drill. The shape is determined by the sharpening method. It can be a spiral surface, a conical surface and a flat surface, and any surface that is manually sharpened.
(3) Sub flank: The minor flank is a narrow facet on the outer cylindrical surface of the drill opposite the machined surface.
(4) Main cutting edge: The main cutting edge is the intersection of the rake face (spiral groove surface) and the main flank face. The main twisting edge of the standard twist drill is straight (or nearly straight)
(5) Sub-cutting edge: The minor cutting edge is the intersection of the rake face (the surface of the spiral groove) and the minor flank face (narrow facet), that is, the edge.
(6) Transverse blade: The chisel edge is the intersection of the two main flank faces, which is located at the foremost end of the drill bit, also known as the drill tip.
Geometric parameters of twist drill
the coordinate plane
(1) Cutting plane Ps: is a plane including the cutting speed direction at this point and which is tangent to the surface cut by the cutting edge at this point.
(2) Base surface Pr: The base surface Pr of the selected point on the main cutting edge of the drill bit is a plane passing through this point and perpendicular to the cutting speed at that point. The base surface always passes through the bit axis and is perpendicular to the plane of the cutting speed direction.
the geometric angle of the drill bit
(1) Helix angle: the intersection line between the surface of the spiral groove of the drill bit and the surface of the outer cylinder is a spiral line, and the angle between the spiral line and the axis of the drill bit is called the helix angle of the drill bit, and is recorded as β. (Refer to the textbook)
(2) edge angle and end face inclination
Since the main cutting edge does not pass through the axial line, the blade inclination angle is formed. For each point on the cutting edge, the blade inclination angle is also different, mainly because the base surface of each point is different from the cutting plane. In order to facilitate the description of the concept, we introduce the concept of the face blade inclination.
? Face rake angle: The angle of the end face of the selected point on the main cutting edge is the angle between the base surface of the point measured in the end projection view and the main cutting edge. For different selected points, the inclination angle of the end face is also different, and the maximum at the outer edge (the absolute value is the smallest) is small near the core (the absolute value is large).
(3) Top (front) angle and lead angle:
The apex angle of the drill bit is the angle between the projections of the two major cutting edges in the plane measured in a plane parallel to the two major cutting edges. Recorded as 2φ, standard twist drill 2φ=118°
The lead angle is the angle between the projection of the main cutting edge and the feed direction measured in the base surface, denoted as κrx. Since the base faces of the points on the main cutting edge are different, the principal off angles at the respective points are also different.
(4) Front angle: The rake angle of the selected point on the main cutting edge is measured in the orthogonal plane of the point.
Reference material
(5) Back angle: The selected relief angle on the main cutting edge is measured in a tangent plane with the bit axis as the axis and passing through the cylindrical surface at that point, denoted as αf.
Third, other drill bits
Carbide twist drill
When machining hard and brittle materials, the use of carbide drills can significantly improve cutting efficiency.
The following hard alloy twist drills are made into a monolithic structure, which can be made into a straight shank carbide hard twist drill, which can be used as a taper shank carbide hard twist drill.
Compared with the high-speed steel twist drill, the core has a larger diameter, a smaller helix angle, and a shorter working portion. The cutter body is made of 9SiCr alloy steel and hardened to 50-52HRC. These measures are designed to improve the rigidity and strength of the drill bit to reduce the chipping caused by vibration during drilling.
(2) Deep hole drilling
Deep pores generally refer to pores having a pore length to diameter ratio greater than 5 times. When drilling deep holes, it is necessary to solve the problems of chip breaking and chip removal, cooling and lubrication, and guiding.
the gun drill
The gun drill was originally used for the bore of the barrel, so it was called the gun hole drill. It is often used to machine small diameter deep hole machining.
1, structure and working principle
The gun drill consists of a cutting part and a drill pipe. The cutting part is made of high-speed steel or hard alloy, and makes the chip flute; the drill pipe is made of seamless steel pipe, and the chip flute is rolled close to the drill bit, and the diameter of the drill pipe is 0.5~1 mm smaller than the diameter of the drill bit. They are joined together by welding and the chip flutes are aligned during welding.
Working principle: the workpiece rotates while drilling, and the drill bit feeds. The cutting fluid is injected into the cutting zone from the inner hole of the drill pipe and the oil inlet hole of the cutting portion by high pressure to cool and lubricate and the chips are flushed out from the chip flute. Since the chips are discharged from the outside of the drill bit, they are called external chips.
2, characteristics
(1) Since the cutting fluid enters and exits separately, the cutting fluid is undisturbed under high pressure and easily reaches the cutting zone, which better solves the problem of cooling and lubrication when drilling deep holes;
(2) Since the cutting edge is divided into inner and outer cutting edges, and the cutting edge has an eccentricity e, the chipping action can be performed during cutting, the chips are narrowed, and the cutting fluid is convenient for punching out the chips, so that the chip discharging is easy;
(3) Since the core column with a diameter of 2h is left after drilling, this can ensure that the support surface of the drill bit is always in close contact with the wall of the hole, so that the drill bit has a reliable guide and solves the problem of guiding the deep hole drill.
Second, the internal chip removal deep hole drilling
The drill bit consists of a drill body, three cutting edges distributed over different circumferences and two guide blocks.
During operation, the high-pressure cutting fluid is sent to the cutting zone from the gap between the drill pipe and the hole wall to provide cooling and lubrication. At the same time, the chips are flushed out from the inner chip hole of the drill bit and the inner hole of the drill pipe.
This deep hole drill, because the three teeth are arranged on different circumferences, acts as a chip to facilitate chip evacuation. Moreover, when the chips are discharged, they do not rub against the machined surface, so the production efficiency and the processing quality are higher than those of the outer chip. This structure has no chisel edge, which reduces the axial force. The unbalanced circumferential force and radial force are received by the guide block on the circumference, and the deep hole drill has better guiding property.
The spray drill
The suction drill consists of three parts: a drill bit, an inner tube and an outer tube.
During operation, 2/3 of the cutting fluid is fed into the cutting zone through the gap between the inner and outer tubes for cooling and lubrication. The remaining 1/3 of the cutting fluid is sprayed into the tube through the narrow slit of the crescent groove on the inner tube wall, so that the pressure difference between the front end and the rear end of the inner tube creates a “suction force” to accelerate the discharge of cutting fluid and chips.