The performance of tool breakage
1) Cutting edge micro collapse
When the material structure, hardness and allowance of workpiece are not uniform, the front angle is too large, the cutting edge strength is low, the rigidity of the process system is insufficient to produce vibration, or intermittent cutting is carried out. If the grinding quality of the cutting edge is not good, the cutting edge is prone to micro collapse, that is, the edge area appears small collapse, notch or peeling. In this case, the tool will lose part of its cutting capacity, but it will continue to work. In the process of continuous cutting, the damaged part of the blade area may expand rapidly, leading to greater damage.
2) Chipping of cutting edge or tip
This kind of damage is often produced under the cutting conditions which is worse than the micro collapse of cutting edge, or the further development of micro collapse. The size and range of the broken tool are larger than that of the micro collapse, which makes the tool completely lose cutting ability and has to stop working. The case of a knife tip breaking is often called a tip drop.
3) Broken blade or tool
When the cutting conditions are extremely bad, the cutting amount is too large, there is impact load, and there is micro crack in the blade or tool material. When welding and grinding exist residual stress in the blade, and the operation is not careful, the blade or tool may break. After this kind of damage, the tool can not be used continuously, so it can be scrapped.
4) Blade surface peeling off
For materials with high brittleness, such as cemented carbide, ceramics, PCBN with high tic content, the surface layer is easy to peel off due to defects or potential cracks in the surface structure, or residual stress in the surface due to welding and edge grinding. The peeling may occur on the front surface, and the knife may occur on the back side. The peeling object is flaky and the peeling area is large. The possibility of coating tool peeling is high. After the blade is slightly peeled, it can continue to work, and the cutting ability will be lost after serious peeling.
5) Plastic deformation of cutting parts
Because of the low strength and low hardness, plastic deformation may occur in the cutting parts of the steel and high speed steel. When the cemented carbide works directly at high temperature and three-way compressive stress, the surface plastic flow will also occur, even the plastic deformation surface of cutting edge or cutting edge will collapse. Collapse usually occurs when cutting amount is large and hard material is processed. The elastic modulus of TiC based cemented carbide is smaller than that of WC based cemented carbide, so the former has faster plastic deformation resistance or failure. The plastic deformation of PCD and PCBN will not occur.
6) Hot crack of blade
When the tool is subjected to alternating mechanical and thermal loads, the surface of the cutting part will inevitably produce alternating thermal stress due to repeated thermal expansion and contraction, which will cause the blade to crack due to fatigue. For example, when the carbide milling cutter is in high speed milling, the teeth are constantly subjected to periodic impact and alternating thermal stress, and the comb cracks appear on the front face. Although some tools do not have obvious alternating load and alternating stress, because of the temperature of surface and inner layer is inconsistent, thermal stress will also be generated. In addition, there are inevitable defects in the inner part of tool materials, so the blade may also produce cracks. Sometimes the tool can continue to work for a while after the crack is formed, sometimes the rapid crack growth causes the blade to break or the blade surface is seriously flaking.
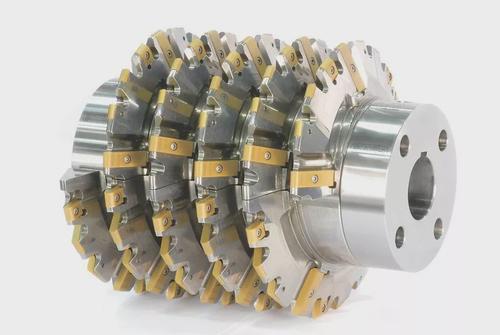
Tool wearing
according to the reasons for wear, it can be divided into:
1) Abrasive wear
There are some very hard particles in the processed materials, which can draw grooves on the surface of the tool, which is abrasive grinding damage. Abrasive wear exists on all sides, and the front surface is the most obvious. But for low speed cutting, the wear of hemp is not obvious because of the low cutting temperature, so abrasive wear is the main reason. The lower the hardness of the other tool, the more serious the abrasive hemp damage.
2) Cold welding wear
During cutting, there is a great pressure and strong friction between the workpiece, cutting and front and rear cutter surface, so cold welding will occur. Because of the relative movement between friction pairs, the cold welding will produce fracture and be taken away by one side, which will cause the cold welding wear. The wear of cold welding is usually serious at medium cutting speed. The results show that brittle metal has better cold welding resistance than plastic metal; The multiphase metal is smaller than that of one-way metal; The tendency of metal compound is smaller than that of single cold welding; The cold welding tendency of group B and iron in the periodic table of chemical elements is small. The cold welding of high speed steel and cemented carbide is serious when cutting at low speed.
3) Diffusion wear
In the process of cutting and contact between workpiece and tool at high temperature, the chemical elements of both sides spread in solid state, which changed the composition structure of the tool, made the surface of the tool vulnerable and intensified the wear of the tool. The diffusion phenomenon always keeps the object with high depth gradient continuously spreading to the object with low depth gradient. For example, cobalt in cemented carbide will rapidly spread to chip and workpiece at 800 ℃, and WC is decomposed into tungsten and carbon to steel; When the cutting temperature of PCD tool is higher than 800 ℃, the carbon atoms in PCD will transfer to the workpiece surface with a great diffusion strength, and the tool surface will be graphitized. The diffusion of cobalt and tungsten is serious, and the diffusion resistance of titanium, tantalum and niobium is strong. Therefore, YT cemented carbide has good wear resistance. When the temperature of ceramic and PCBN is as high as 1000 ℃ -1300 ℃, diffusion wear is not significant. Because of the same material, the workpiece, chip and tool will generate thermal potential in the contact area during cutting. This thermoelectric potential can promote diffusion and accelerate the wear of the tool. This kind of diffusion wear under the action of thermoelectric potential is called “thermoelectric wear”.
4) Oxidation wear
When the temperature increases, the surface oxidation of the tool produces soft oxide, which is caused by chip friction, which is called oxidation wear. For example, oxygen in the gas at 700 ℃ ~800 ℃ reacts with cobalt, carbide and titanium carbide in cemented carbide to form soft oxides; The chemical reaction of PCBN with water vapor at 1000 ℃
according to the wear form, it can be divided into:
Front face damage
When cutting plastic materials at a large speed, the front cutting surface near the cutting force will wear into crescent denture under the action of chip cutting, so it is also called crescent groove wear. In the early stage of wear, the front angle of the tool increases, which improves the cutting conditions and is conducive to the curl and fracture of the chip. However, when the crescent groove is further increased, the cutting edge strength is greatly weakened, which may eventually cause the breakage and damage of the cutting edge. When cutting brittle materials, or cutting plastic materials with lower cutting speed and thinner cutting thickness, crescent wear will not occur.
Wear of the blade tip
The wear of the tip is the wear on the back surface of the arc of the tip and the adjacent back side of the tool. It is the continuation of the wear on the back blade surface of the tool. Because of the poor heat dissipation conditions and stress concentration, the wear speed is faster than the back blade surface. Sometimes a series of grooves with spacing equal to the feed amount will be formed on the back of the pair cutter surface, which is called groove wear. They are mainly caused by the hardened layer and cutting pattern of the machined surface. When cutting hard cutting materials with a large hardening tendency, the groove wear is the most likely. The wear of the tool tip has the greatest influence on the surface roughness and machining accuracy of the workpiece.
Wear of rear cutter surface
When cutting plastic materials with large cutting thickness, the back face of the tool may not contact the workpiece due to the presence of chip lumps. In addition, the back face usually contacts the workpiece, and a wear belt with a rear angle of 0 is formed on the back surface. Generally, in the middle of the working length of the cutting edge, the wear of the back face is even, so the wear degree of the back face can be measured by VB of the width of the wear belt of the back cutting edge. Because the wear of various types of tools almost occurs in different cutting conditions, especially when cutting brittle materials or cutting plastic materials with a small cutting thickness, the wear of the tool is mainly the back surface wear, and the measurement of the width VB of the wear belt is relatively simple, so VB is usually used to represent the wear degree of the tool. The larger VB, not only increases the cutting force, causes the cutting vibration, but also affects the wear of the arc of the tool tip, thus affecting the machining accuracy and the surface quality.
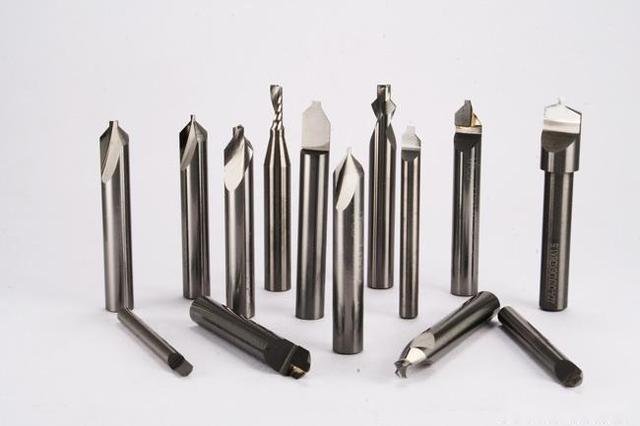
methods for preventing the tool from being damaged
1) According to the characteristics of the processed materials and parts, the various types and brands of the tool materials are selected reasonably. Under the premise of certain hardness and wear resistance, the necessary toughness of the tool material must be ensured;
2) The geometric parameters of the tool are selected reasonably. By adjusting the front and rear angles, the main and secondary deflection angles, the blade inclination angle and other angles;
Ensure that the cutting edge and the cutting edge have good strength. Grinding out the negative chamfering on the cutting edge is an effective measure to prevent the tool from falling;
3) Ensure the quality of welding and grinding, and avoid defects caused by poor welding and edge grinding. The tool used in key process shall be grinded to improve the surface quality and check for cracks;
4) The cutting amount should be selected reasonably to avoid excessive cutting force and too high cutting temperature, so as to prevent the tool from being damaged;
5) The process system is as rigid as possible and vibration can be reduced;
6) Take correct operation method to avoid or reduce sudden load of tool.
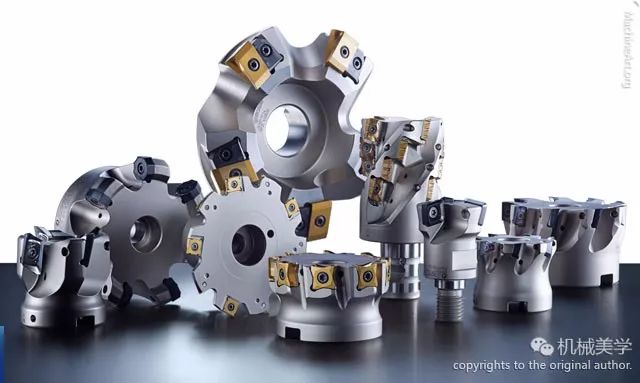
The cause and Countermeasure of tool breakage
1) The blade brand and specification are not selected properly, such as the thickness of the blade is too thin or the brand is too hard and brittle when rough processing.
Countermeasures:
The brand with high bending strength and toughness is selected to increase the thickness of the blade or install the blade vertically.
2) The tool geometry parameters are not selected properly (such as too large front and rear angles).
Countermeasures:
The tool can be redesigned from the following aspects.
① Reduce the front and rear corners properly.
② The larger negative blade angle is adopted.
③ Decrease the main deflection angle.
④ Adopt larger negative chamfering or edge arc.
⑤ Repair and grind the transition cutting edge to enhance the cutting edge.
3) The welding process of blade is incorrect, which causes excessive welding stress or welding crack.
Countermeasures:
① Avoid the use of three-sided closed blade groove structure.
② Solder is selected correctly.
③ Avoid heating welding with oxyacetylene flame and keep it warm after welding to eliminate internal stress.
④ Use mechanical clamping structure as much as possible
4) The grinding stress and crack are caused by improper grinding method; The vibration of the teeth after grinding the PCBN milling cutter is too large, which makes the load of individual teeth too heavy, and also causes the tool beating.
Countermeasures:
① The grinding is performed by intermittent grinding or diamond grinding wheel.
② Soft grinding wheel is selected and the grinding wheel is kept sharp.
③ Pay attention to the quality of the grinding and strictly control the vibration and swing of the cutter teeth.
5) Unreasonable cutting quantity selection, such as too much, the machine tool is boring; When cutting intermittently, the cutting speed is too high, the feed is too large, and the blank allowance is not uniform, the cutting depth is too small; When cutting materials with high hardness tendency, such as high manganese steel, the feed rate is too small.
Countermeasures:
Re select the cutting amount.
6) The reasons of the uneven bottom surface of the cutting groove or the long extension of the blade are the reasons of the mechanical clamping tool.
Countermeasures:
① Trim the bottom of the knife groove.
② The position of cutting fluid nozzle should be arranged reasonably.
③ The hardened cutter rod adds cemented carbide gasket under the blade.
7) Excessive tool wear.
Countermeasures:
Change the cutting edge or change the cutting edge in time.
8) The cutting fluid flow is insufficient or the filling method is incorrect, which causes the blade to burst hot and crack.
Countermeasures:
① Increase the flow of cutting fluid.
② The position of cutting fluid nozzle should be arranged reasonably.
- Effective cooling methods such as spray cooling are used to improve the cooling effect.
④ The * cutting is used to reduce the impact on the blade.
9) The tool is not installed correctly, such as: the cutting tool is too high or too low; The end milling cutter adopts asymmetric milling.
Countermeasures:
Refit the tool.
10) The rigidity of the process system is too poor, which causes too much vibration of cutting.
Countermeasures:
① Increase the auxiliary support of the workpiece and improve the clamping rigidity of the workpiece.
② Reduce the overhang length of the tool.
③ Reduce the back angle of the tool properly.
④ Other vibration suppression measures shall be adopted.
11) Improper operation, such as: tool cut in from the middle of the workpiece, too strong action; Stop before you have returned the knife.
Countermeasures:
Pay attention to the operation method.
4、 Chip tumor
1) Causes of formation
In the part near the cutting edge, the contact area of the cutter chip is very high, so that the bottom metal of the chip is embedded in the micro uneven peak valley on the front cutter surface, forming a real metal contact without gap and thus the bonding phenomenon occurs. This part of the knife chip contact area is called the bonding area. In the bonding area, a thin layer of metal material will be deposited on the front cutting surface at the bottom of the chip. The metal materials of this part of the chip have undergone severe deformation and strengthened at the appropriate cutting temperature. With the continuous outflow of chips, the stagnant material will slip away from the upper layer of chip, which is the basis of chip tumor. Then, a second layer of stagnant cutting material will be formed on it, which will form debris deposits.
2) Characteristics and influence on cutting
① The hardness is 1.5-2.0 times higher than that of the workpiece material, which can replace the front tool surface for cutting. It can protect the cutting edge and reduce the front tool surface wear. However, debris flowing through the contact area of the tool workpiece will cause the back face wear of the tool.
② The working angle of the tool increases after the chip forming, which plays an active role in reducing the chip deformation and cutting force.
③ Because the chip lumps protrude outside the cutting edge, the actual cutting depth increases, which affects the dimension accuracy of the workpiece.
④ The chip deposit will cause “ploughing” phenomenon on the surface of the workpiece, which will affect the surface roughness of the workpiece. ⑤ The debris of the chip tumor will bond or embed into the surface of the workpiece, which will cause hard points, which will affect the quality of the machined surface.
From the above analysis, it can be seen that chip accumulating tumor is unfavorable to cutting and finishing.
3) Control measures
The following measures can be taken to avoid the chip tumor without binding or deformation strengthening between the bottom material and the front cutting surface.
① Reduce the roughness of the front cutter surface.
② Increase the front angle of the tool.
③ Reduce the cutting thickness.
④ Low speed cutting or high-speed cutting is adopted to avoid cutting speed which is easy to form chip forming.
⑤ The hardness and plasticity of the workpiece materials are improved by proper heat treatment.
⑥ The cutting fluid with good anti adhesion property (such as extremely pressure cutting fluid with sulfur and chlorine) is adopted.