1.Processing characteristics of gray iron
Gray cast iron has the characteristics of brittleness and low tensile strength (cast iron structure can be regarded as iron-carbon alloy structure filled with graphite pores. The presence of flake graphite reduces the ductility and toughness of cast iron) and is a typical brittle material.
The graphite cavity structure of flake graphite in gray cast iron is easy to form cracks with sharp edges. During cutting, under the action of the cutting force of the tool, the crack develops along the direction of minimum resistance, resulting in chipping and fracture of the chip. Therefore, the gray cast iron forms breakable chipping chips during the cutting process. At the same time, the tool is in the intermittent cutting working state during the processing of the gray cast iron. When the graphite in the base body is cut, the tool is in the idle state, and the metal is cut. In the case of the base body, the cutting action of the tool occurs, and the tool continuously cuts into and cuts out, causing the high-frequency pulling and compressive stress cycles of the tool near the cutting edge. The alternating load causes the surface layer of the tool to fatigue and causes slight chipping at the cutting edge, reducing The cutting performance of the tool.
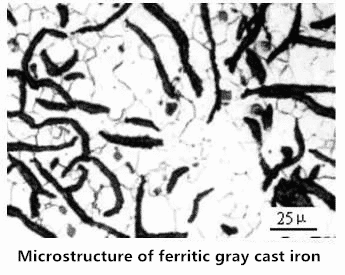
During the cutting process, the cut gray cast iron structure frequently breaks irregularly, causing an unstable change in the cutting force and a large impact on the cutting edge. When the gray cast iron is cut, typical chipping chips are generated. The deformation coefficient of the chip is small, and the contact length of the chip is extremely short, so that the cutting force and the cutting heat are concentrated in a small area of the cutting edge, and the tool has thermal shock wear.
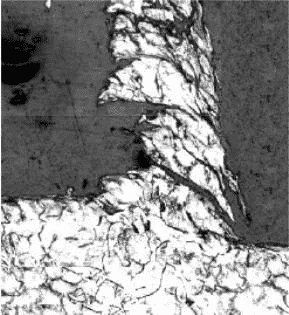
The chipping debris and the falling carbide hard spots generated by the cutter when cutting gray cast iron often cause the surface of the workpiece and the back blade to grind, resulting in wear of the flank VB abrasive; the cutting temperature is obviously increased once the flank face is worn, The fine chipping and chipping easily enters the chipping interface. Under high temperature and high pressure, the iron element in the chip and the surface of the tool and the tool surface form an infinite replacement solid solution, resulting in diffusion wear, while the chip softens and adheres to the tool surface. The wear surface forms a uniform layer of adhesion resulting in bond wear. Once the edge of the cutting tool wears or chipping, the cutting force is sharply increased, the surface quality of the workpiece has been significantly reduced, and the edge is prone to breakage or collapse, which is easy to collapse;
2.The effect of main cutting angles
The 90 degrees of the main cutting angles will radially introduce the feed force into the thinner part of the workpiece material;
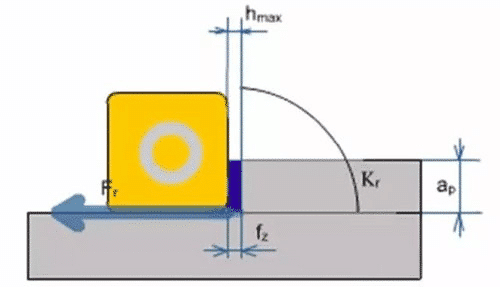
45 degrees of main cutting angles will direct the force to the material supported by the wider base;
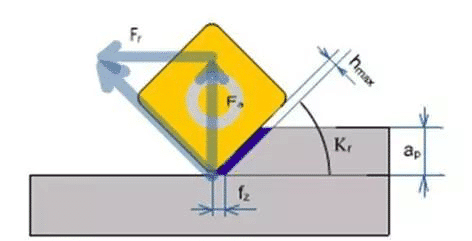
Gaps and burrs occur when the feed force exceeds the material strength. Brittle materials such as cast iron tend to have gaps, while more tough workpiece materials tend to have burrs. More tough workpiece materials often have burrs. It directs the feed force to the tougher part of the workpiece material. This reduces or eliminates the formation of workpiece nicks or burrs.
3.Effect of different cutting edge grooves
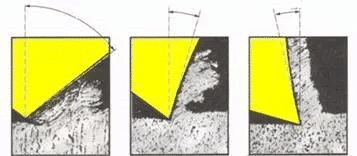
The use of a sharp grooved blade can effectively reduce the cutting force and reduce the occurrence of chipping. At this time, fz is limited by the average chip thickness of the blade. Try to choose a blade type with good strength but sharp edge (cutting light groove shape, large front angle, sharp but strong strength blade type (smaller blade width T), during roughing, if in working condition When it is not stable, when the large fz (more than 0.2) is used, the phenomenon of chipping will be aggravated, especially when the tool cuts in and cuts out the workpiece. After the blade wears more than 0.3, this phenomenon is also the same. Will increase.
4.The effect of different materials
Physical vapor deposition (PVD), coating applications are thinner and suitable for relatively sharp cutting edges. The coating increases lubricity and helps reduce the cutting forces generated between the tool and the workpiece, making the cutting relatively light. Especially for the edge collapse phenomenon during finishing, there will be a great improvement.
5.Other factors
In the current machining market, for the processing of cast iron materials, from the actual processing results, the tool life of ductile iron materials (mainly burrs) (below QT450) is better than that of gray iron (mainly workpiece chipping). Workpiece chipping and burrs lead to a large factor in tool change. In addition to the 45 degrees lead angle we often use, the sharp-groove type of blade is used, which is relatively small for each tooth. It also strengthens the clamping rigidity of the workpiece itself (adding auxiliary support to weak parts), and can also change the position of the tool and so on.
Deja una respuesta
Tu dirección de correo electrónico no será publicada.