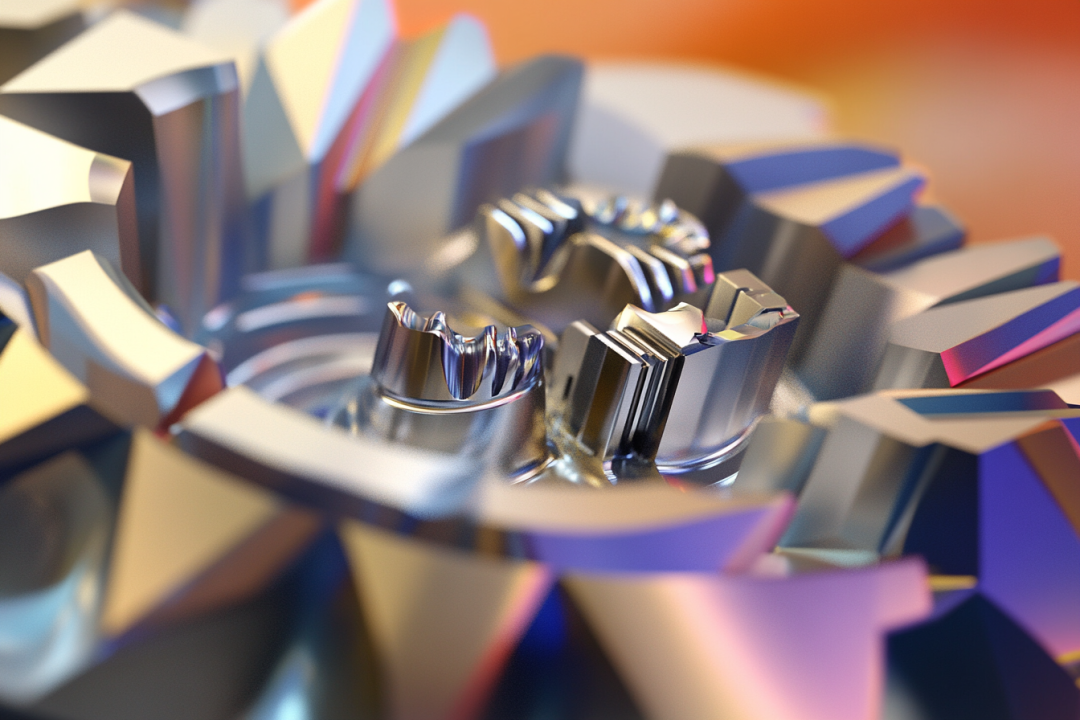
Cemented carbide cutting tools are very common in cutting operations, and the correct selection of cutting tools is crucial for ensuring processing efficiency and quality. By familiarizing ourselves with the composition ratio of cutting tool materials, we can select the appropriate tools to meet different machining requirements. Therefore, Zhangzhiyuan has compiled a list of 10 main materials and their common proportions to help find the best cutting tools.
Carbon Tungsten Carbide
Tungsten carbide is a material used for manufacturing cutting tools and is the primary material due to its ultra-high hardness and wear resistance, allowing the tools to remain sharp during high-intensity cutting processes.
(1) 60% – 70% Tungsten Carbide
Used for cutting tools that require higher toughness and impact strength, suitable for processing softer or more ductile materials.
① Suitable for processing: aluminum alloys, copper alloys, plastics, low-carbon steel, medium-carbon steel, etc.
② Suitable conditions: rough machining tools, such as turning tools, milling cutters, and tools for heavy cutting.
③ Representative tools: Sandvik GC4030 turning blade, Kennametal KCP25 series milling blade, etc.
(2) 70% – 80% Tungsten Carbide
Used for multi-functional cutting tools, balancing hardness and toughness, suitable for a wide range of cutting applications.
① Suitable for processing: stainless steel, alloy steel, tool steel, cast iron, etc.
② Suitable conditions: medium machining tools, such as general turning tools, milling cutters, and drilling cutters.
③ Representative tools: Sandvik GC1125 series blade, Kennametal KCPK30 milling blade.
(3) 80% – 85% Tungsten Carbide
Used for cutting tools with high hardness and wear resistance, suitable for processing harder metal materials.
① Suitable for processing: hardened steel, high-strength alloy steel, tool steel, and heat-resistant alloys, etc.
② Suitable conditions: finishing tools, high-speed cutting tools, and tools for difficult-to-machine materials, such as precision turning tools and high-speed milling cutters.
(4) 85% – 90% Tungsten Carbide
Used for cutting tools that require extremely high hardness and wear resistance, suitable for high-intensity and high-speed cutting applications.
① Suitable for processing: hardened steel, superhard alloys, titanium alloys, and nickel-based alloys, and other high-strength materials.
② Suitable conditions: high-hardness cutting tools, such as high-speed cutting tools used in aerospace and automotive manufacturing, and finishing tools that require extremely high wear resistance.
(5) 90% – 95% Tungsten Carbide
Used for cutting tools with ultra-high hardness and extreme wear resistance, suitable for processing very hard materials.
① Suitable for processing: superhard alloys, hardened steel, hard cast iron, and other high-hardness materials.
② Suitable conditions: ultra-precision machining tools, high-precision cutting tools, especially suitable for applications that require extreme wear resistance, such as mold manufacturing and precision machining of hard materials.
Cobalt Powder
Cobalt powder is a binder used in cemented carbide cutting tools that provides toughness and impact resistance, commonly used to balance the hardness and wear resistance of the tools.
(1) 3% – 6% Cobalt Powder
Used for cutting tools that require higher hardness and wear resistance, typically applied in finishing and high-speed cutting.
① Suitable for processing: high-strength alloy steel, hardened steel, stainless steel, etc.
② Suitable conditions: finishing tools, high-speed cutting tools, such as high-speed milling cutters and turning tools.
(2) 6% – 10% Cobalt Powder
This is the most common proportion range, suitable for multi-purpose tools, balancing hardness, toughness, and wear resistance, applicable to a wide range of cutting applications.
① Suitable for processing: general steel, cast iron, stainless steel, heat-resistant alloys, etc.
② Suitable conditions: turning tools, milling cutters, and drilling cutters, particularly suitable for processing medium to high-strength materials.
(3) 10% – 15% Cobalt Powder
Used for cutting tools that require higher toughness and impact strength, suitable for rough machining and heavy cutting tasks.
① Suitable for processing: high-hardness alloy steel, large castings, heat-resistant alloys, and other hard materials.
② Suitable conditions: rough machining tools, such as heavy cutting milling cutters, turning tools, and drills, especially used under high impact and high stress conditions.
(4) 15% – 25% Cobalt Powder
Used in specific cases, such as cutting tools that require extremely high toughness and impact resistance, particularly suitable for tools used under extreme heavy-duty cutting conditions.
① Suitable for processing: high-strength alloy steel, superhard materials, and other materials that require extremely high toughness and impact resistance.
② Suitable conditions: tools for rough machining, milling cutters with large cutting depths, turning tools, and cutting tools used under heavy-duty conditions.
Titanium Aluminum Carbide
Titanium aluminum carbide is a compound formed by titanium, aluminum, and carbon elements, commonly used as a coating or blended material for cemented carbide cutting tools to enhance hardness, wear resistance, and oxidation resistance.
(1) Ti-Al-C Ratio 1:1:1
This ratio of titanium aluminum carbide is typically used for high-temperature resistant coatings and structural materials, offering excellent high-temperature stability and hardness, suitable for cutting processes in high-temperature environments.
① Suitable for processing: high-temperature alloys, heat-resistant steels, stainless steels, and other materials.
② Suitable conditions: tools that require high-temperature and wear resistance, such as high-speed cutting tools, drills, and milling cutters.
(2) Ti-Al-C Ratio 2:1:1
With a higher titanium content in this ratio, the material’s toughness and oxidation resistance are enhanced, making it suitable for high-speed cutting and the processing of medium-strength materials.
① Suitable for processing: stainless steels, titanium alloys, heat-resistant alloys, etc.
② Suitable conditions: multi-purpose tools, such as turning tools, milling cutters, and drilling cutters, particularly suitable for processing medium-strength materials.
(3) Ti-Al-C Ratio 3:1:2
This ratio increases the proportion of aluminum, improving the material’s high-temperature and corrosion resistance performance, making it suitable for applications that require high oxidation resistance.
① Suitable for processing: ultra-high-temperature alloys, difficult-to-machine materials, corrosion-resistant alloys, etc.
② Suitable conditions: cutting tools used under extreme conditions, such as cutting tools for the aerospace industry and tools for processing high-temperature alloys.
Nickel Powder
Nickel powder is a binder material commonly used in cemented carbide cutting tools that enhances the toughness and corrosion resistance of the tools, particularly suitable for use in environments with high processing requirements.
(1) Nickel Content 10% – 15%
This proportion of nickel powder is used to improve the corrosion resistance and toughness of cutting tools, suitable for processing non-ferrous metals and corrosion-resistant materials.
① Suitable for processing: aluminum alloys, copper alloys, stainless steels, and other materials.
② Suitable conditions: tools for precision machining and those that require high corrosion resistance, such as milling cutters and drills.
(2) Nickel Content 15% – 20%
At this ratio, the higher nickel content enhances the tool’s impact resistance and toughness, suitable for heavy-duty machining and cutting of difficult-to-machine materials.
① Suitable for processing: heat-resistant alloys, high-strength steels, stainless steels, etc.
② Suitable conditions: tools for heavy cutting and rough machining, suitable for processing under high-stress conditions.
(3) Nickel Content 20% – 25%
This proportion of nickel powder is used for tools that require extremely high toughness and durability, suitable for high-intensity machining under extreme conditions.
① Suitable for processing: ultra-high-strength alloys, difficult-to-machine materials, and materials that require fatigue resistance.
② Suitable conditions: high-precision tools and heavy-duty machining tools, applicable in fields such as aerospace and nuclear industries.
Trace Elements
Titanium
Titanium is a lightweight, high-strength metal material with excellent corrosion resistance and biocompatibility. It is commonly used in the coatings and substrates of cemented carbide cutting tools to enhance the tool’s strength, wear resistance, and oxidation resistance.
(1) Titanium Content 10% – 15%
This proportion of titanium is used to enhance the wear resistance and strength of cutting tools, particularly suitable for use under high-temperature and high-stress conditions.
① Suitable for processing: stainless steels, titanium alloys, high-temperature alloys, and other materials.
② Suitable conditions: high-precision tools, high-temperature cutting tools, such as coated tools and milling cutters.
(2) Titanium Content 15% – 20%
At this ratio, the higher content of titanium is suitable for processing environments that require high strength and impact resistance.
① Suitable for processing: high-strength steels, nickel-based alloys, corrosion-resistant alloys, etc.
② Suitable conditions: heavy-duty machining tools, high-temperature resistant tools, particularly suitable for cutting applications in the aerospace and energy fields.
(3) Titanium Content 20% – 25%
This high proportion of titanium is mainly used to enhance the stability and durability of tools under extreme machining conditions, suitable for cutting difficult-to-machine materials.
① Suitable for processing: ultra-high-temperature alloys, difficult-to-machine metals, composite materials, etc.
② Suitable conditions: cutting tools used in extreme environments, such as tools for the nuclear industry, aerospace, and military applications.
Tantalum
Tantalum is a rare metal with a high melting point and good thermal conductivity, commonly used in the coatings and alloy compositions of cemented carbide cutting tools to enhance the tool’s wear resistance, heat resistance, and corrosion resistance, especially suitable for high-temperature and heavy-duty cutting environments.
(1) Tantalum Content 5% – 10%
This proportion of tantalum is used to enhance the wear resistance and thermal stability of cutting tools, suitable for cutting processes under medium to high temperatures.
① Suitable for processing: stainless steels, alloy steels, titanium alloys, etc.
② Suitable conditions: medium to high-temperature cutting tools, such as coated tools and milling cutters, applicable in industries like aerospace, automotive manufacturing, etc.
③ Representative tools: Iscar IC5500 series blades, Kennametal KCU15 blade.
(2) Tantalum Content 10% – 15%
At this ratio, the moderate content of tantalum further improves the tool’s corrosion resistance and oxidation resistance, suitable for use at even higher temperatures.
① Suitable for processing: high-temperature alloys, corrosion-resistant steels, stainless steels, etc.
② Suitable conditions: coated tools for extreme conditions, high-strength turning tools, particularly suitable for the energy and aviation fields.
③ Representative tools: Walter WKP35 series blades, Sandvik GC4225 blade.
(3) Tantalum Content 15% – 20%
This high proportion of tantalum is used for extreme high-temperature and heavy-duty cutting applications, ensuring that the tools maintain high performance under harsh processing conditions.
① Suitable for processing: ultra-high-temperature alloys, difficult-to-machine metals, wear-resistant materials.
② Suitable conditions: high-temperature coated tools for the nuclear industry and aerospace fields, heavy-duty milling cutters for extreme machining conditions.
Chromium
Chromium is a hard metal with good corrosion resistance and wear resistance, commonly used in the coatings and alloys of cemented carbide cutting tools to enhance the tool’s wear resistance, corrosion resistance, and oxidation resistance, particularly suitable for use under severe processing conditions.
(1) Chromium Content 5% – 10%
This proportion of chromium is used to enhance the tool’s wear resistance and corrosion resistance, suitable for moderate-intensity cutting applications.
① Suitable for processing: stainless steels, alloy steels, cast irons, etc.
② Suitable conditions: cutting tools with moderate strength, such as general turning tools and milling cutters.
(2) Chromium Content 10% – 15%
At this ratio, the increased content of chromium improves the tool’s oxidation resistance and durability, suitable for higher temperature and more severe processing environments.
① Suitable for processing: high-temperature alloys, corrosion-resistant steels, nickel-based alloys, etc.
② Suitable conditions: high-temperature cutting tools, corrosion-resistant coated tools, applicable in aerospace and energy fields.
(3) Chromium Content 15% – 20%
This high proportion of chromium is used for tools that require extremely high wear resistance and corrosion resistance, especially for processing at extreme temperatures.
① Suitable for processing: ultra-high-temperature alloys, corrosion-resistant alloys, hard metals, etc.
② Suitable conditions: high-temperature coated tools for the nuclear industry and aerospace fields, heavy-duty cutting tools for extreme conditions.
Niobium
Niobium is a rare metal with a high melting point, excellent heat resistance, and corrosion resistance. It is commonly used in the coatings of cemented carbide cutting tools or added as an alloying element to enhance the tool’s stability and oxidation resistance during high-temperature and high-intensity processing.
(1) Niobium Content 5% – 10%
This proportion of niobium is used to enhance the tool’s thermal stability and oxidation resistance, suitable for cutting operations under medium to high temperatures.
① Suitable for processing: stainless steels, titanium alloys, nickel-based alloys, etc.
② Suitable conditions: high-temperature cutting tools and corrosion-resistant coated tools, such as turning and milling cutters.
(2) Niobium Content 10% – 15%
At this ratio, the increased content of niobium significantly enhances the tool’s high-temperature strength and fatigue resistance, suitable for use under extreme processing conditions.
① Suitable for processing: high-temperature alloys, corrosion-resistant steels, stainless steels, etc.
② Suitable conditions: high-strength turning tools, heavy-duty milling cutters, especially suitable for high-demand fields such as aerospace and nuclear industries.
(3) Niobium Content 15% – 20%
This high proportion of niobium is used for tools that require extremely high heat resistance and oxidation resistance, particularly suitable for use in ultra-high temperatures and extreme processing conditions.
① Suitable for processing: ultra-high-temperature alloys, corrosion-resistant alloys, composite materials, etc.
② Suitable conditions: high-temperature coated tools under extreme environments, high-precision cutting tools, especially applicable in nuclear and aerospace industries.
Vanadium
Vanadium is a metal element used to enhance the wear resistance and oxidation resistance of cutting tools. It is commonly added as an alloying additive or coating material to cemented carbide cutting tools to improve their performance during high-temperature and high-intensity processing.
(1) Vanadium Content 5% – 10%
This proportion of vanadium is used to enhance the tool’s wear resistance and oxidation resistance, suitable for cutting operations under medium to high temperatures.
① Suitable for processing: alloy steels, stainless steels, high-temperature alloys, etc.
② Suitable conditions: for turning and milling cutters, especially for high-temperature cutting and applications requiring high corrosion resistance.
(2) Vanadium Content 10% – 15%
At this ratio, the increased content of vanadium further improves the tool’s high-temperature strength and wear resistance, suitable for processing under extreme conditions.
① Suitable for processing: high-strength steels, corrosion-resistant alloys, nickel-based alloys, etc.
② Suitable conditions: for heavy-duty turning tools, milling cutters, especially for cutting under high-temperature and high-stress conditions.
(3) Vanadium Content 15% – 20%
This high proportion of vanadium is used for tools that require extremely high wear resistance and oxidation resistance, particularly suitable for use in ultra-high temperatures and extreme processing conditions.
① Suitable for processing: ultra-high-temperature alloys, corrosion-resistant materials, composite materials, etc.
② Suitable conditions: for high-temperature coated tools under extreme environments, high-precision cutting tools, especially applicable in aerospace and energy fields.
Titanium Carbide of Cutting tools
Titanium carbide is an ultra-hard material commonly used as a coating or as an alloy component in cemented carbide cutting tools. It significantly improves the tool’s hardness, wear resistance, and high-temperature performance, making it suitable for cutting operations in high-intensity and high-temperature environments.
(1) Titanium Carbide Content 10% – 15%
This proportion of titanium carbide is used to enhance the tool’s wear resistance and thermal resistance, suitable for cutting at high temperatures.
① Suitable for processing: stainless steels, alloy steels, titanium alloys, etc.
② Suitable conditions: for high-speed milling and turning tools, especially in cases where high wear resistance is required.
③ Representative tools: Sandvik GC1125 series blades, Walter WKK10 series blades.
(2) Titanium Carbide Content 15% – 20%
At this ratio, the content of titanium carbide is further increased, significantly improving the tool’s hardness and wear resistance, suitable for processing under extreme conditions.
① Suitable for processing: high-temperature alloys, hard metals, nickel-based alloys, etc.
② Suitable conditions: for heavy-duty cutting tools, precision milling cutters, especially for processing under high-temperature and high-stress conditions.
(3) Titanium Carbide Content 20% – 25%
This high proportion of titanium carbide is used for tools that require extremely high hardness and heat resistance, particularly suitable for use in extreme high-temperature and heavy-duty processing conditions.
① Suitable for processing: ultra-high-temperature alloys, composite materials, corrosion-resistant materials, etc.
② Suitable conditions: for high-temperature coated tools in aerospace, nuclear industry, and other fields, as well as high-precision cutting tools.
Gaining a deep understanding of the proportions of tool materials and making the optimal choice using a rational and scientific approach inherently reflects the scientific spirit of cutting machining professionals. The scientific spirit is not only about the thirst for knowledge and rigor in details, but also about the dedication to technological research and the pursuit of precision. Upholding the scientific spirit, cutting machining professionals continuously drive the progress of the manufacturing industry.What are the important proportions of cemented carbide materials?